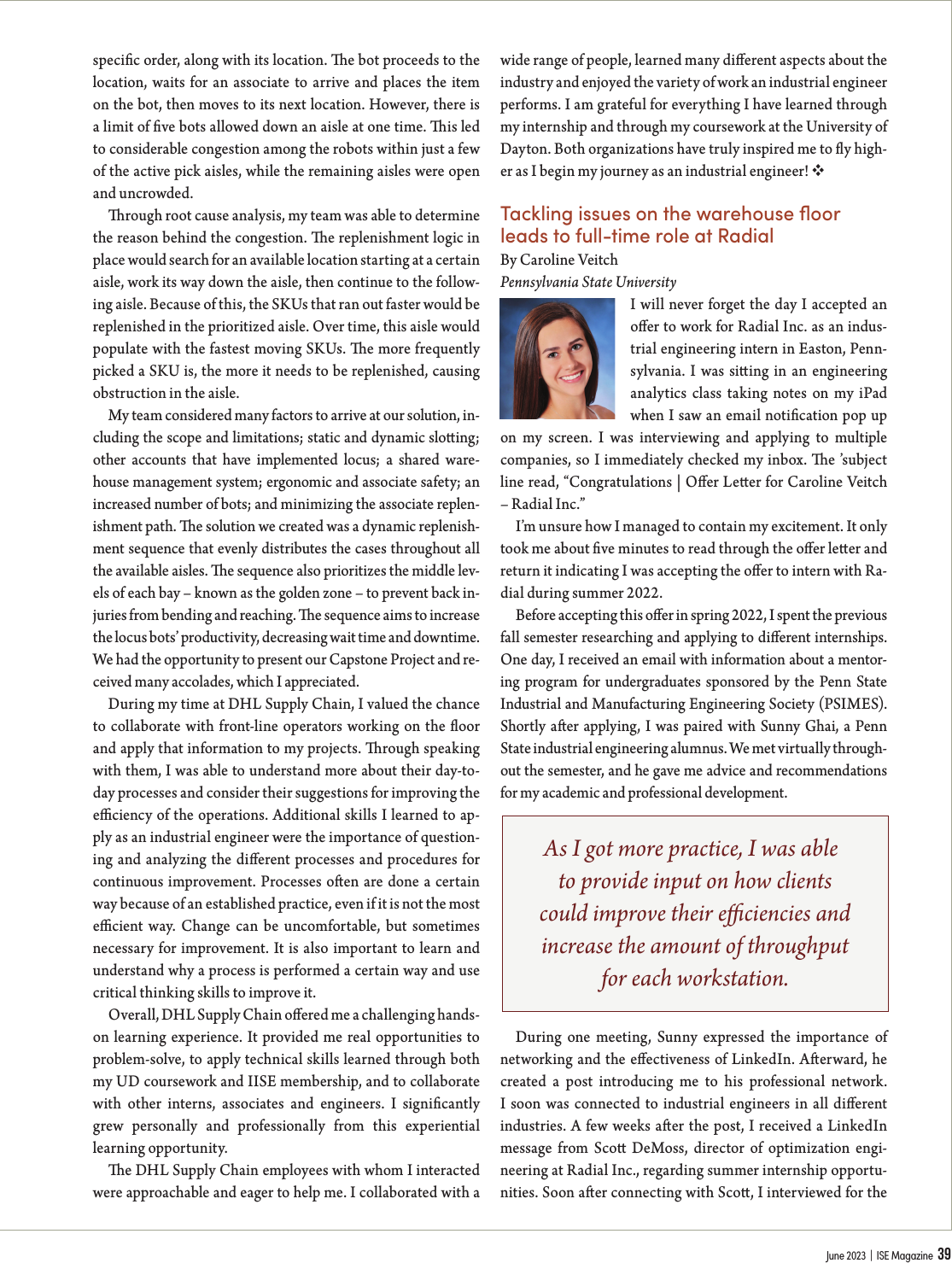
June 2023 | ISE Magazine 39
specic order, along with its location. e bot proceeds to the
location, waits for an associate to arrive and places the item
on the bot, then moves to its next location. However, there is
a limit of ve bots allowed down an aisle at one time. is led
to considerable congestion among the robots within just a few
of the active pick aisles, while the remaining aisles were open
and uncrowded.
rough root cause analysis, my team was able to determine
the reason behind the congestion. e replenishment logic in
place would search for an available location starting at a certain
aisle, work its way down the aisle, then continue to the follow-
ing aisle. Because of this, the SKUs that ran out faster would be
replenished in the prioritized aisle. Over time, this aisle would
populate with the fastest moving SKUs. e more frequently
picked a SKU is, the more it needs to be replenished, causing
obstruction in the aisle.
My team considered many factors to arrive at our solution, in-
cluding the scope and limitations; static and dynamic sloing;
other accounts that have implemented locus; a shared ware-
house management system; ergonomic and associate safety; an
increased number of bots; and minimizing the associate replen-
ishment path. e solution we created was a dynamic replenish-
ment sequence that evenly distributes the cases throughout all
the available aisles. e sequence also prioritizes the middle lev-
els of each bay – known as the golden zone – to prevent back in-
juries from bending and reaching. e sequence aims to increase
the locus bots’ productivity, decreasing wait time and downtime.
We had the opportunity to present our Capstone Project and re-
ceived many accolades, which I appreciated.
During my time at DHL Supply Chain, I valued the chance
to collaborate with front-line operators working on the oor
and apply that information to my projects. rough speaking
with them, I was able to understand more about their day-to-
day processes and consider their suggestions for improving the
eciency of the operations. Additional skills I learned to ap-
ply as an industrial engineer were the importance of question-
ing and analyzing the dierent processes and procedures for
continuous improvement. Processes oen are done a certain
way because of an established practice, even if it is not the most
ecient way. Change can be uncomfortable, but sometimes
necessary for improvement. It is also important to learn and
understand why a process is performed a certain way and use
critical thinking skills to improve it.
Overall, DHL Supply Chain oered me a challenging hands-
on learning experience. It provided me real opportunities to
problem-solve, to apply technical skills learned through both
my UD coursework and IISE membership, and to collaborate
with other interns, associates and engineers. I signicantly
grew personally and professionally from this experiential
learning opportunity.
e DHL Supply Chain employees with whom I interacted
were approachable and eager to help me. I collaborated with a
wide range of people, learned many dierent aspects about the
industry and enjoyed the variety of work an industrial engineer
performs. I am grateful for everything I have learned through
my internship and through my coursework at the University of
Dayton. Both organizations have truly inspired me to y high-
er as I begin my journey as an industrial engineer!
Tackling issues on the warehouse floor
leads to full-time role at Radial
By Caroline Veitch
Pennsylvania State University
I will never forget the day I accepted an
oer to work for Radial Inc. as an indus-
trial engineering intern in Easton, Penn-
sylvania. I was siing in an engineering
analytics class taking notes on my iPad
when I saw an email notication pop up
on my screen. I was interviewing and applying to multiple
companies, so I immediately checked my inbox. e ’subject
line read, “Congratulations | Oer Leer for Caroline Veitch
– Radial Inc.”
I’m unsure how I managed to contain my excitement. It only
took me about ve minutes to read through the oer leer and
return it indicating I was accepting the oer to intern with Ra-
dial during summer 2022.
Before accepting this oer in spring 2022, I spent the previous
fall semester researching and applying to dierent internships.
One day, I received an email with information about a mentor-
ing program for undergraduates sponsored by the Penn State
Industrial and Manufacturing Engineering Society (PSIMES).
Shortly aer applying, I was paired with Sunny Ghai, a Penn
State industrial engineering alumnus. We met virtually through-
out the semester, and he gave me advice and recommendations
for my academic and professional development.
During one meeting, Sunny expressed the importance of
networking and the eectiveness of LinkedIn. Aerward, he
created a post introducing me to his professional network.
I soon was connected to industrial engineers in all dierent
industries. A few weeks aer the post, I received a LinkedIn
message from Sco DeMoss, director of optimization engi-
neering at Radial Inc., regarding summer internship opportu-
nities. Soon aer connecting with Sco, I interviewed for the
As I got more practice, I was able
to provide input on how clients
could improve their eciencies and
increase the amount of throughput
for each workstation.